In the fast-evolving world of industrial operations, downtime can be costly, often resulting in production halts and increased maintenance expenses. Traditional maintenance methods, which rely on scheduled checks or reactive repairs, are no longer sufficient in this age of technological advancements. This is where Predictive Maintenance (PdM) powered by the Internet of Things (IoT) comes into play—a cutting-edge solution that has revolutionized the way industries approach equipment management.
Predictive Maintenance, fueled by IoT sensors and real-time data analytics, not only enhances operational efficiency but also saves time, money, and resources. Let’s explore how this combination is driving industrial innovation and boosting productivity.
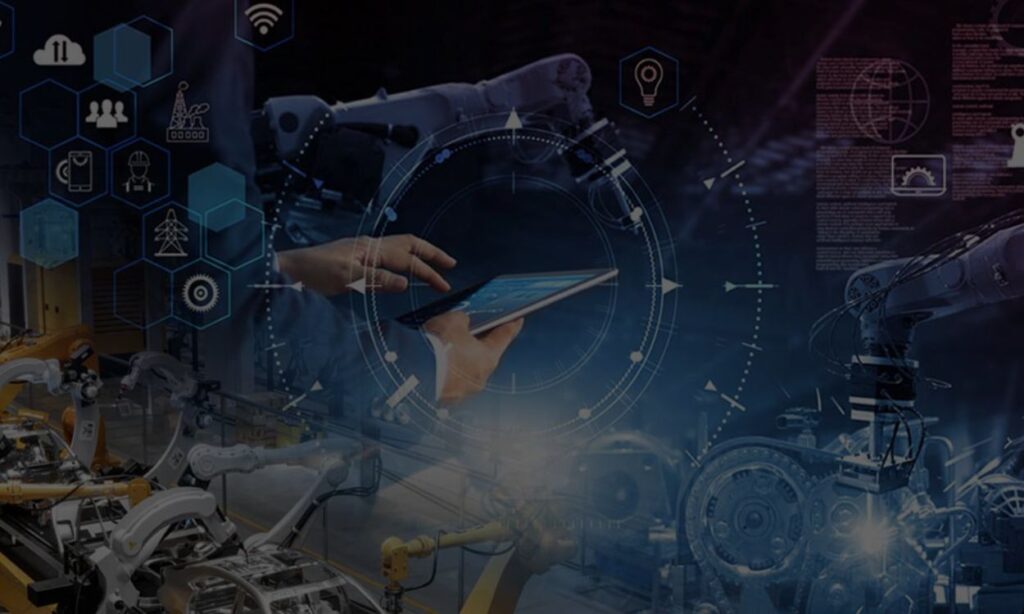
Understanding Predictive Maintenance
Predictive Maintenance is a proactive approach to asset management that leverages data-driven insights to predict when equipment is likely to fail. Instead of relying on routine or reactive maintenance practices, PdM uses sensor-generated data and machine learning algorithms to monitor the real-time health of machinery and predict potential issues.
By continuously tracking performance metrics such as temperature, vibration, humidity, and pressure, the system detects anomalies and sends alerts before a breakdown occurs. This allows technicians to take preventive actions, thereby minimizing unplanned downtime and optimizing maintenance schedules.
The Role of IoT in Predictive Maintenance
The Internet of Things plays a crucial role in making Predictive Maintenance more effective and scalable. IoT devices, primarily sensors, are embedded in industrial machines to collect vast amounts of data. These sensors monitor the critical parameters of equipment and send this data to cloud-based platforms for analysis.
Here are Some Key Contributions of IoT to Predictive Maintenance:
1. Real-Time Monitoring
IoT sensors enable real-time monitoring of equipment, ensuring that any deviations from normal operations are instantly detected. For instance, a sudden rise in temperature could indicate motor overheating, prompting immediate attention before a major failure occurs.
2. Data-Driven Insights
IoT collects enormous data sets that are analyzed by AI algorithms. These insights offer a clear picture of the machinery’s condition, allowing maintenance teams to predict failures with high accuracy. The data-driven approach ensures maintenance activities are targeted and efficient, reducing unnecessary interventions.
3. Remote Diagnostics
With IoT-based PdM, companies can monitor their assets from anywhere. Remote diagnostics enable teams to assess issues without being physically present on-site, reducing travel time and enhancing response efficiency.
4. Integration with Cloud Platforms
Cloud computing serves as the backbone for IoT-driven predictive maintenance. It provides the infrastructure to store, process, and analyze sensor data in real-time. This integration allows businesses to automate workflows, schedule timely repairs, and optimize their supply chain for replacement parts.
4 Benefits of Predictive Maintenance with IoT
Implementing Predictive Maintenance through IoT offers numerous advantages to industrial operations. Let’s break down some of the key benefits:
1. Minimizing Downtime
Predictive Maintenance allows industries to address issues before they escalate into major problems. By scheduling maintenance activities based on equipment health, companies can avoid unexpected breakdowns, ensuring smoother production cycles.
2. Cost Efficiency
Regular maintenance or unexpected failures can significantly inflate operational costs. With IoT, industries can minimize both labor and material costs by carrying out maintenance only when necessary. It reduces the need for spare parts and ensures the optimal use of resources.
3. Extended Asset Lifespan
Monitoring machines in real-time enables businesses to keep equipment running at optimal performance, thereby extending the lifespan of assets. This reduces the frequency of replacements and enhances return on investment.
4. Improved Safety
IoT-based PdM ensures that equipment operates within safe parameters, reducing the risk of accidents caused by malfunctioning machinery. This creates a safer working environment for employees and avoids potential legal and financial liabilities.
SIOTA
SIOTA – IoT Automation Services offers cutting-edge solutions to streamline industrial operations through smart IoT integration. From real-time equipment monitoring to predictive maintenance, SIOTA’s services help businesses reduce downtime, optimize performance, and increase efficiency. With remote diagnostics, data-driven insights, and automated workflows, SIOTA empowers companies to make informed decisions and maintain peak operational health, delivering scalable and cost-effective industrial automation tailored to modern business needs.
Wrapping Up
Predictive Maintenance, driven by IoT, is transforming the way industries manage their assets. The ability to monitor equipment in real-time, predict failures, and optimize maintenance schedules is a game-changer for industrial efficiency. By embracing this technology, businesses can significantly reduce downtime, save costs, and improve overall productivity.
As the industrial sector becomes more reliant on automation and data-driven decision-making, integrating Predictive Maintenance with IoT will continue to be a cornerstone of operational success. The future of industrial maintenance is here—and it’s smart, efficient, and connected.
Don’t Miss: IoT-Based LPG Monitoring: Enhancing Fuel Efficiency and Safety